Minimal Subsurface Oxidation
Studies show that dry hydrogen peroxide exhibits self-limiting behavior on Si, SiGe and TiN surfaces. Anhydrous hydrogen peroxide (HOOH) readily splits into OH radicals, ensuring a high concentration of -OH groups on the surface that serves as a large diffusion barrier. It is difficult for additional HOOH to penetrate this barrier. In contrast, HOH (water) splits into -H and -OH groups on the surface, resulting in low –OH population and a poor barrier for additional water to react.
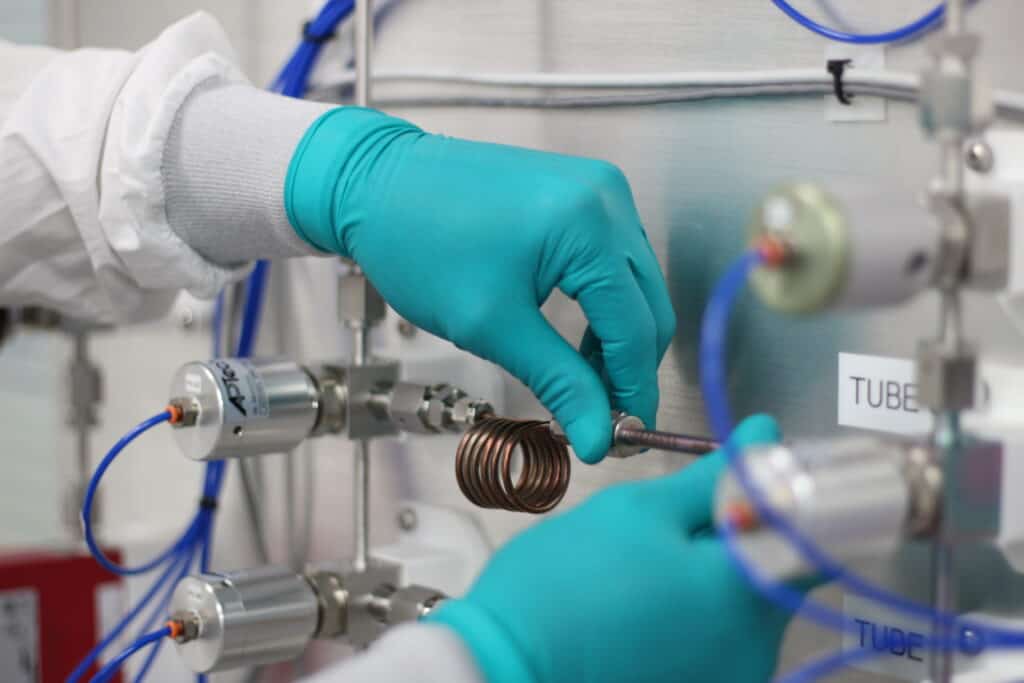
Cure of Gap Fill Dielectric Films
As devices shrink, transistors become smaller, making it difficult to physically and electrically isolate their structures. Aspect ratios can exceed 100:1 and structures can have a highly complex profiles. Void-free gap-fill in these structures is critical for better performance of advanced devices.
Oxidation Rate
As structures become taller and narrower, oxidation of gap-fill film becomes increasingly difficult with conventional oxidants (ozone, water etc.). Ozone forms a crust that slows penetration, leading to lower overall process throughput. Water is a mild oxidant, requiring long cycles. A more effective and reactive oxidant is required to overcome these issues.
Reach Deep Structures
Gap-fill dielectric materials normally contain a large amount of Si-H bonds, which give rise to its hydrophobic property. With hydrogen peroxide vapor, the Si-H can be easily converted to Si-OH and the film becomes hydrophilic.
Temperature and Reactivity
Hydrophilicity allows water vapor penetration into deep structures up to 15 microns. This highly reduces the time required for dielectric formation by accelerating the oxidation rate. In some cases, process time can be reduced by over 20x.
Interfacial Defects Caused by Island Growth
Water vapor can penetrate through deep structures with the aid of hydrogen peroxide vapor. Therefore, the process will no longer require high process temperature. This enables reduced overall thermal budget and less film stress and cracking.
Gate Oxides
Smaller, more efficient devices require highly uniform nucleation, limited subsurface oxidation, and precise film thickness.
Dangling Bonds
When oxides are not deposited uniformly on gate structures, dangling bonds are left behind. This leads to dielectric leakage and poor electrical performance. Risk of this surface degradation associated with water increases with vertical scaling. Ideally, the process oxidant will react with every silicon and hafnium bond, eliminating surface dangling bonds and potential island growth. Hydrogen peroxide has lower steric hindrance than water and naturally forms hydroxyl groups, reducing dangling bonds.
Minimal Subsurface Oxidation
Studies show that dry hydrogen peroxide exhibits self-limiting behavior on Si, SiO2, SiN, and TiN surfaces. Anhydrous hydrogen peroxide (HOOH) readily splits into OH radicals, ensuring a high concentration of -OH groups on the surface that serves as a large diffusion barrier. It is difficult for additional HOOH to penetrate this barrier. In contrast, HOH (water) splits into -H and -OH groups on the surface, resulting in low –OH population and a poor barrier for additional water to react.
Thin-Film Passivation Layer
High quality, thin, low defect interface layers can be created at low temperatures using hydrogen peroxide gas. Passivation layers are ultra-thin so that they do not compromise device properties.
Multiple Patterning
Self-Aligned Multiple Patterning technology has been widely implemented in advanced semiconductor manufacturing processes due to the late arrival and extremely high cost of of EUV technology. As devices shrink, it is a challenge to form a conformal spacer on small 3D & HAR features. Good uniformity and excellent conformality at >20:1 AR are critical for next generation SAMP process.
For multiple patterning applications that require low flows or single wafer applications:
High Volume ALD
The Internet of Things requires low power and high performance semiconductor devices which will only be enabled through new materials and 3D architectures. These new devices must be processed at lower temperatures and without attacking metal surfaces at high throughput. As processes scale, oxidants must also be able to support to high volume ALD challenges.
Low Temperature Oxides
Next generation devices contain highly sensitive metal alloys which cannot be exposed to high temperatures. Traditional water ALD is unreactive or too slow at moderate temperatures. Methods involving ozone or oxygen plasma are overly aggressive and damage the surface. A new oxidant is needed which shows good reactivity (GPC) and deposits high quality oxides without adverse effects.